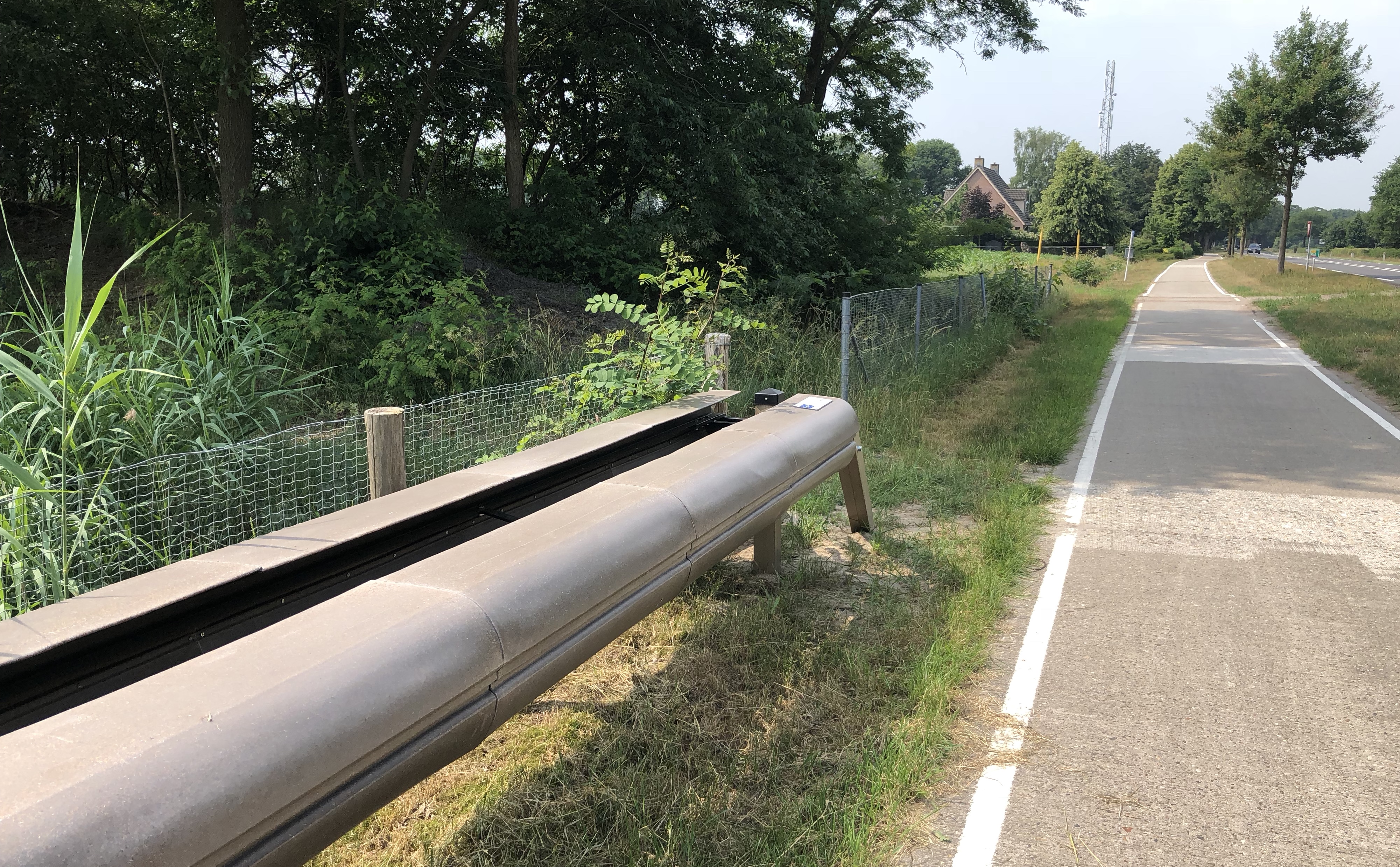
Project update july 2021
After the mock-up of the BG4US LIFE15 2.0 guardrail has been installed in March 2018, the circular biobased guardrail has been further modified to a single sided circular biobased hybrid guardrail to be used for Provincial roads – containment level N2. This modification has resulted in that more circular biobased materials can be applied in our innovative guardrail development.
At the moment, spare parts are manufactured and assembled to see how the installation of our BG4US LIFE15 guardrail should be done under real conditions near the road, once it has been certified. In the parallel, besides the dynamic simulations already performed, pre-crash tests are performed with part of the BG4US construction, using a real car and using different biobased guardrail system set-ups with short lengths (see the Figure below), to learn what can be expected performing the real crash test. Learnings are made with the help of a crash test expert and high speed cameras installed. In the parallel, materials testing are ongoing and a first screening of LCA of the BG4US LIFE15 guardrail are performed. The mechanical properties are a part needed for a technical file to get our innovative guardrail certified, once the crash test has been performed. In autumn 2021, a last pre-crash test is anticipated to be performed, before entering the phase of the real crash test.
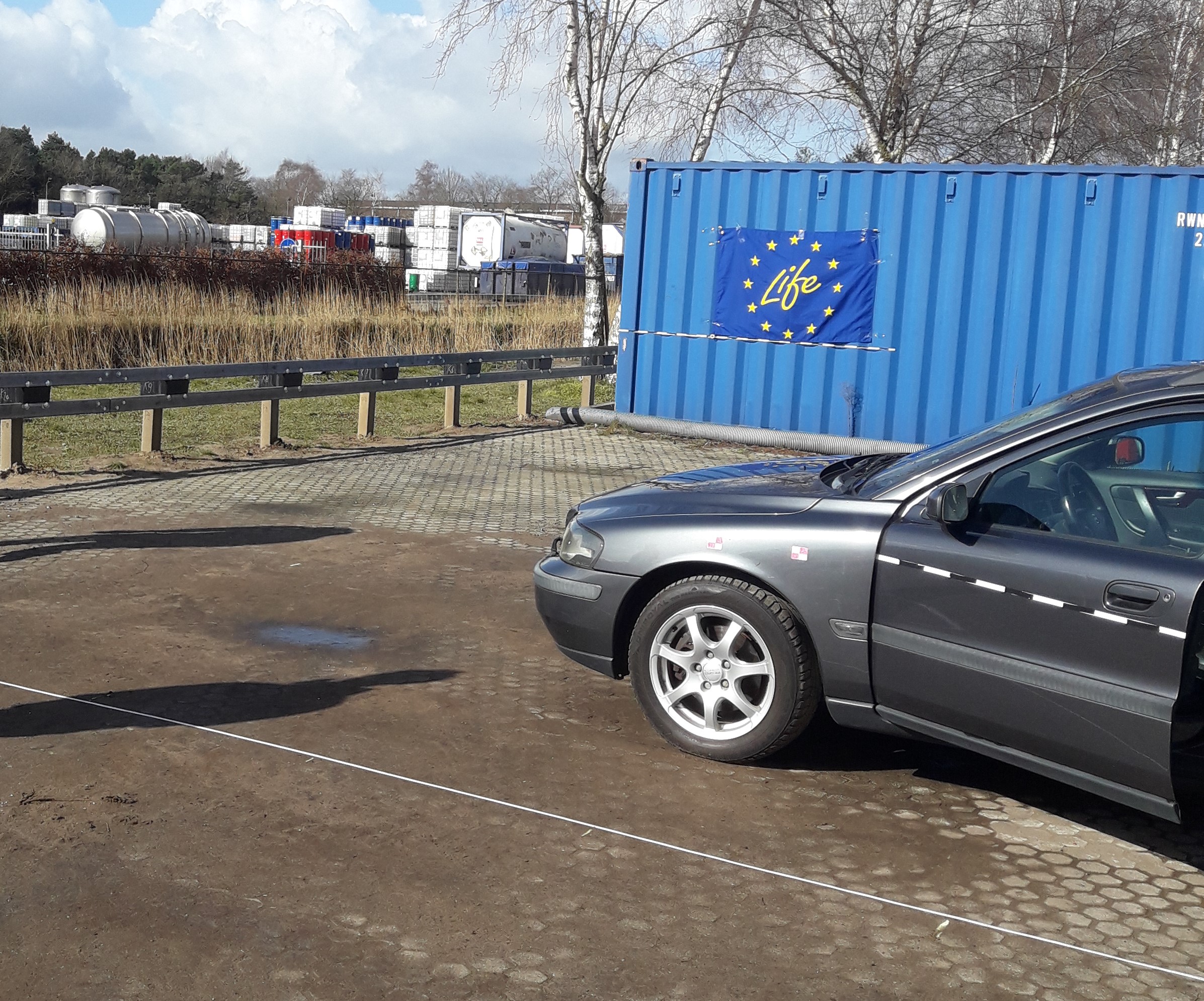
Mock-up 2.0 prototype Guardrail has been installed
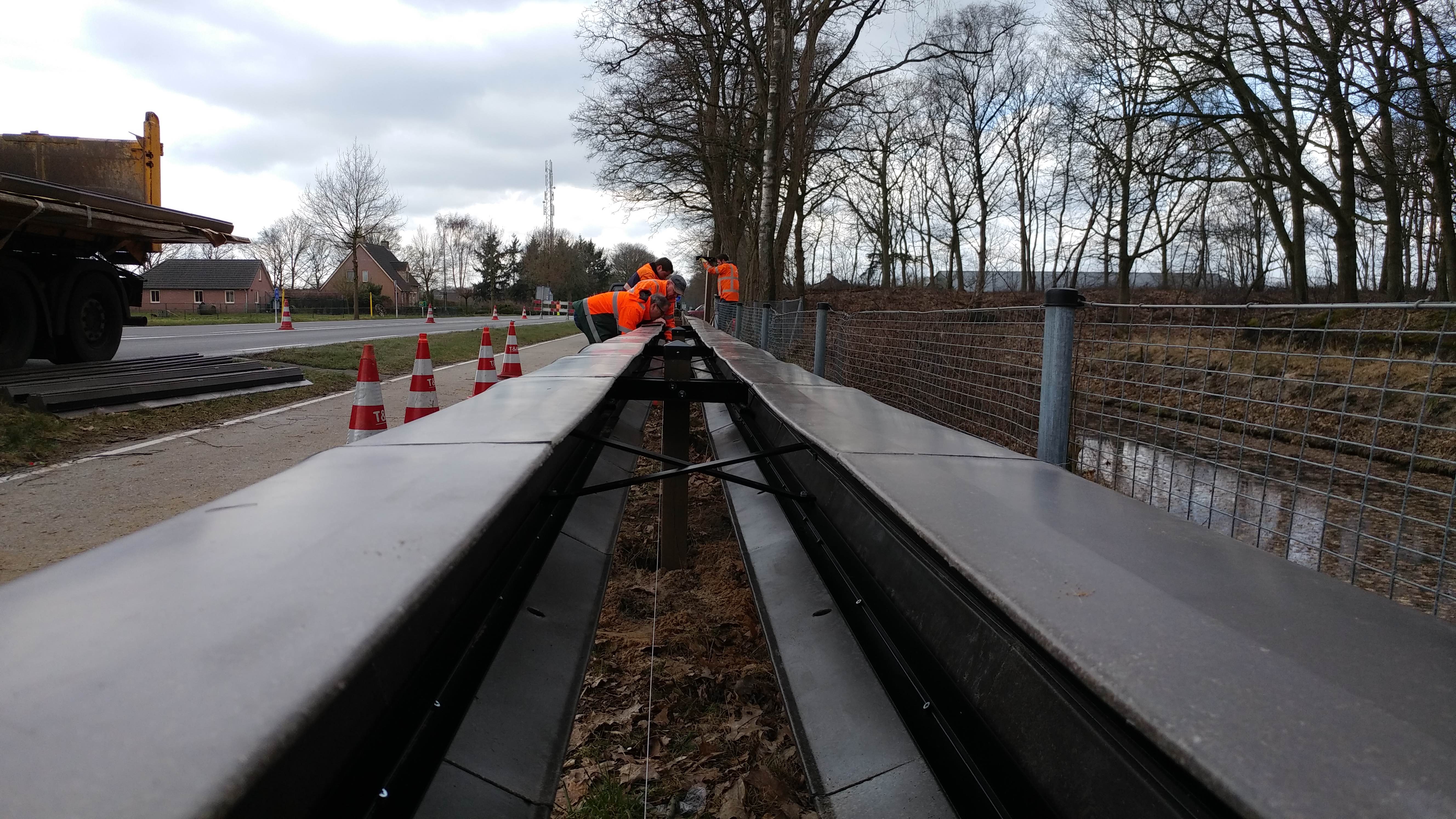
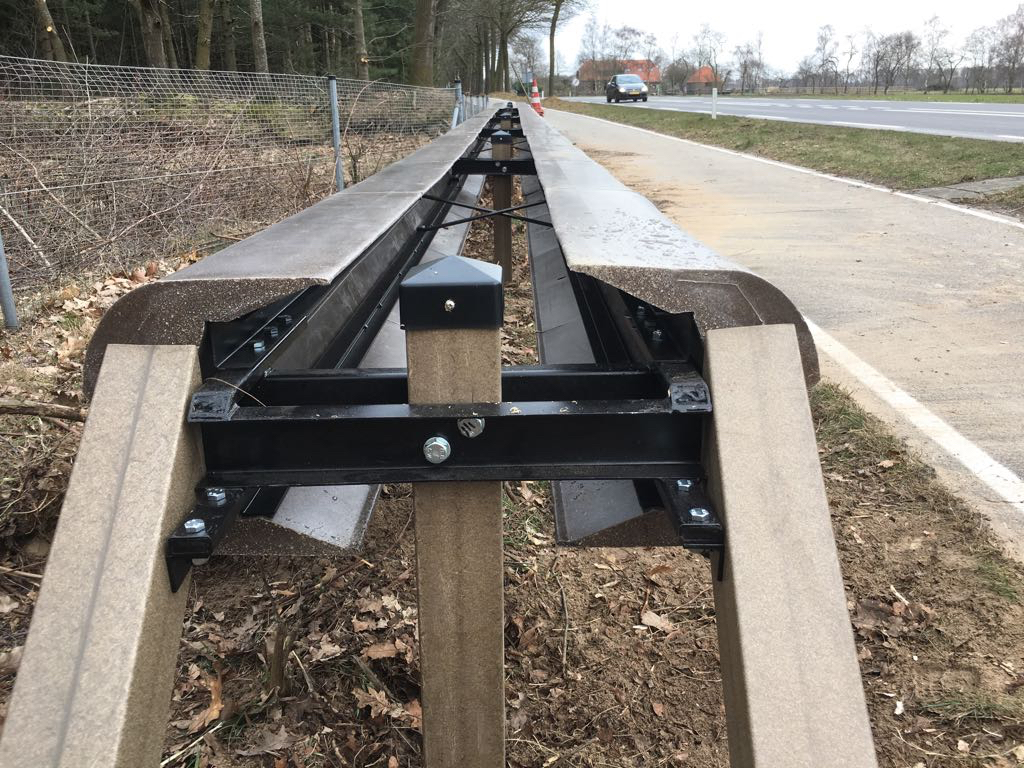
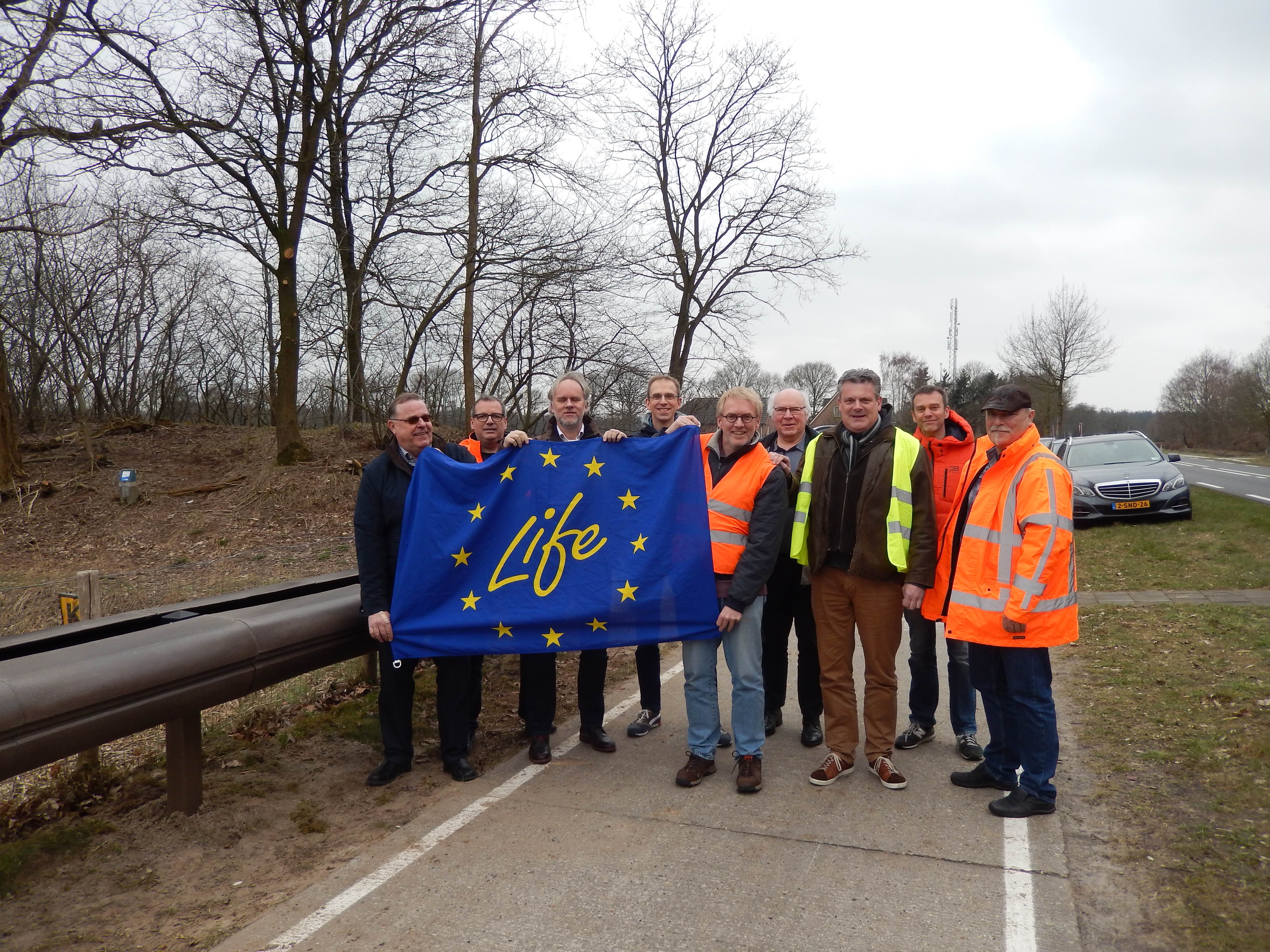